In News:
- From less than 10 MW in 2010, India has added significant Solar photovoltaics (PV) capacity of over 50 GW by 2022, propelling India's push toward cleaner energy generation technologies.
- India is aiming for 280 GW of renewable energy (out of 500 GW by 2030) from solar PV, which will necessitate the deployment of nearly 30 GW of solar capacity each year until 2030.
- However, there are obstacles that must be overcome in order for the PV economy to be sustainable.
What’s in today’s article:
- About solar photovoltaics (PV) economy in India
Solar photovoltaics (PV) economy in India:
About solar PV:
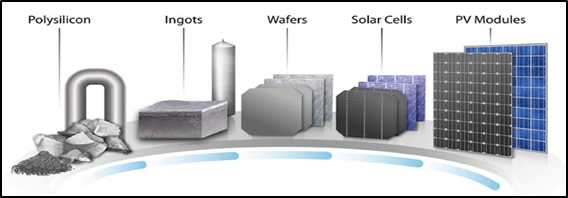
- PV materials and devices convert sunlight into electrical energy.
- A single PV device is known as a cell, which is made of different semiconductor materials (like Silicon).
- A single PV cell is typically small, with a power output of 1 or 2 watts.
- To increase the power output of PV cells, they are chained together to form larger units known as modules or panels, which are sandwiched between glass and/or plastic protective materials.
- Modules can be used individually or in groups to form arrays. As part of a complete PV system, one or more arrays are then connected to the electrical grid.
- The current capacity of solar module manufacturing in India is 15 GW per year.
Challenges faced:
- Heavy dependence on imports:
- Indian companies rely heavily on imports because India currently lacks module and cell manufacturing capacity.
- This is due to a lack of solar wafers (China currently manufactures over 90% of the world's solar wafers) and polysilicon ingots manufacturing.
- For example, India currently produces only 3.5 GW of cells; imports 100% of silicon wafers and around 80% of cells.
- Uncompetitiveness in technology and cost:
- In terms of cell technology, most manufacturing technologies in India can provide efficiencies of 18-19% at the cell level and 16-17% at the module level.
- That is why only 3-4 GW of the 15 GW of module manufacturing capacity is technologically competitive and suitable for grid-based projects.
- The majority of the Indian industry is currently set up to handle small wafer sizes.
- The larger size has an advantage in terms of silicon cost per wafer because it means less silicon loss during ingot to wafer processing.
- Poor raw materials supply:
- Silicon wafer, the most expensive raw material, is not manufactured in India.
- Other key raw materials such as metallic pastes of silver and aluminium to form the electrical contacts, are almost 100% imported.
Current government policy:
- Key initiatives include -
- A 40% duty on the import of modules and 25% duty on the import of cells.
- A production linked incentive (PLI) scheme to support manufacturing capex.
- It is mandatory to procure modules only from an approved list of manufacturers (ALMM) for projects that are connected to state or central government grids. So far only India-based manufacturers have been approved.
Way ahead:
- India is more of an assembly hub than a manufacturing hub, and it would be advantageous in the long run to move up the value chain by producing components.
- It could influence the price and quality of both cells and modules.
- Land, the most expensive component of solar projects, is scarce in India.
- Hence, the Indian industry has no choice but to shift toward newer, superior, innovative and efficient technologies as part of its expansion plans.
- To make the right grade of silicon for solar cell manufacturing, India will need to collaborate on technology.
- India has made few investments in high-quality, high-technology centres like IMEC Belgium or the Holst Centre in the Netherlands, which can assist the industry in trying and testing new technologies at a low cost.
- Academics and industry must collaborate to establish state-of-the-art manufacturing and testing facilities for cells, modules.